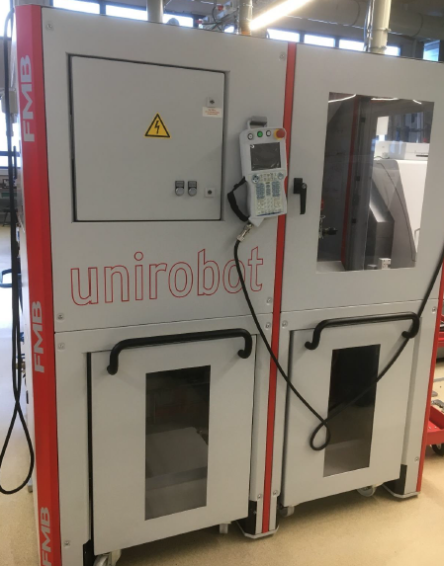
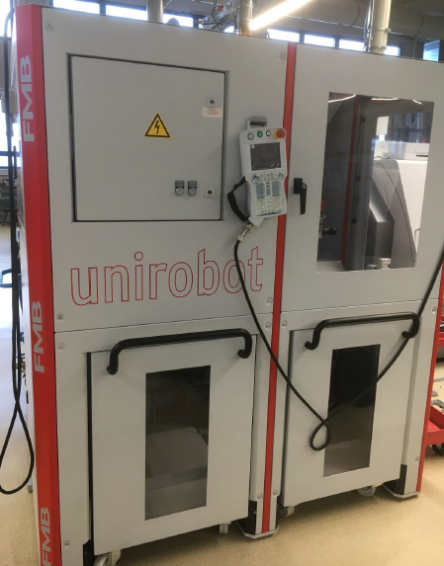
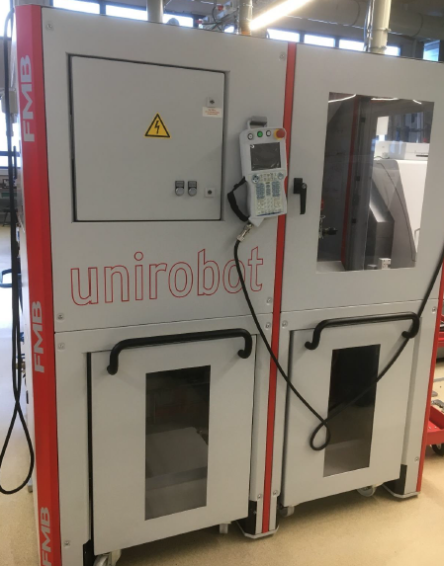
FMB robot cell 2PW with two pallet trucks
Compact automation cell with 2 trolleys for holding the stacked workpiece carriers in the format up to max. 600 x 400 mm and automatic pallet changer.
The loading and unloading system unirobot 2PW is suitable for the automation of CNC-controlled lathes, milling machines, drilling centers, presses, punching and much more.
It is equipped with a modern 6-axis industrial robot, which handles workpiece handling by means of a workpiece-specific gripper system.
FMB unirobot MH5LS-2PW
Production No .: 13-210105
Year of construction: 2014
Operating time: approx. 200 hours (Mint condition, as the machine is in use with bar loader)
Control: FS100
Robot: Yaskawa – 5Kg
Gripper: Schunk two times
Pallets: 20 pieces, approx. 600x400mm
Including pneumatic turning station and workpiece sensor
robot manufacturers – Yaskawa
Robot handling weight – Max. 5 kg
Robot range – 895 mm
construction – movable cell
Workpiece carrier system
Pallet system, cart system
buffer
stacked workpiece carrier 600×400 mm
on wagon
Stack height max. 590 mm
payload – Max. 50 kg per workpiece carrier
The robot cell is mounted in front of the loading door of the machine tool. On a rail system that is anchored to the ground, the robot cell can be moved to set-up and maintenance work on the machine tool.
Three zero point indexing on the rail system enable a positionally accurate fixation of the robot cell after moving back to the working position.
A torsion-resistant steel base frame forms the basis for all installations in the robot cell. The robot cell is provided all around with a protective cover.
Two maintenance doors provide access to the robot cell.
For the supply and removal of workpieces, workpiece carriers in the format max. 600 x 400 mm used. The workpiece carriers are fed in and out via carriages of the robot cell. The robot cell is equipped with two shafts for a blank and a finished part car.
The workpiece carriers are stacked on the blank cart up to a maximum height of 590 mm.
A pallet changer handles the handling of the workpiece carriers.
The pallet changer retrieves the workpiece carriers from the blank carriage with raw parts and places them on the work plane of the robot for removal and insertion of the workpieces into the machine tool. The machined workpiece carriers with finished parts are then stacked on the precast trailer.
Optionally, the robot cell can be equipped with a separating bulkhead, which separates the loading space from the working space of the robot and thus enables a change of the car even during the working process.
The robot control is integrated in the base frame, so that for the entire unit a space requirement of only 1,800 x 1,200 mm plus 1.000 mm displacement is required.
All functions of the robot cell are operated and programmed via a compact, user-friendly handheld programming device with touch screen.
Further information can be found in the attachment